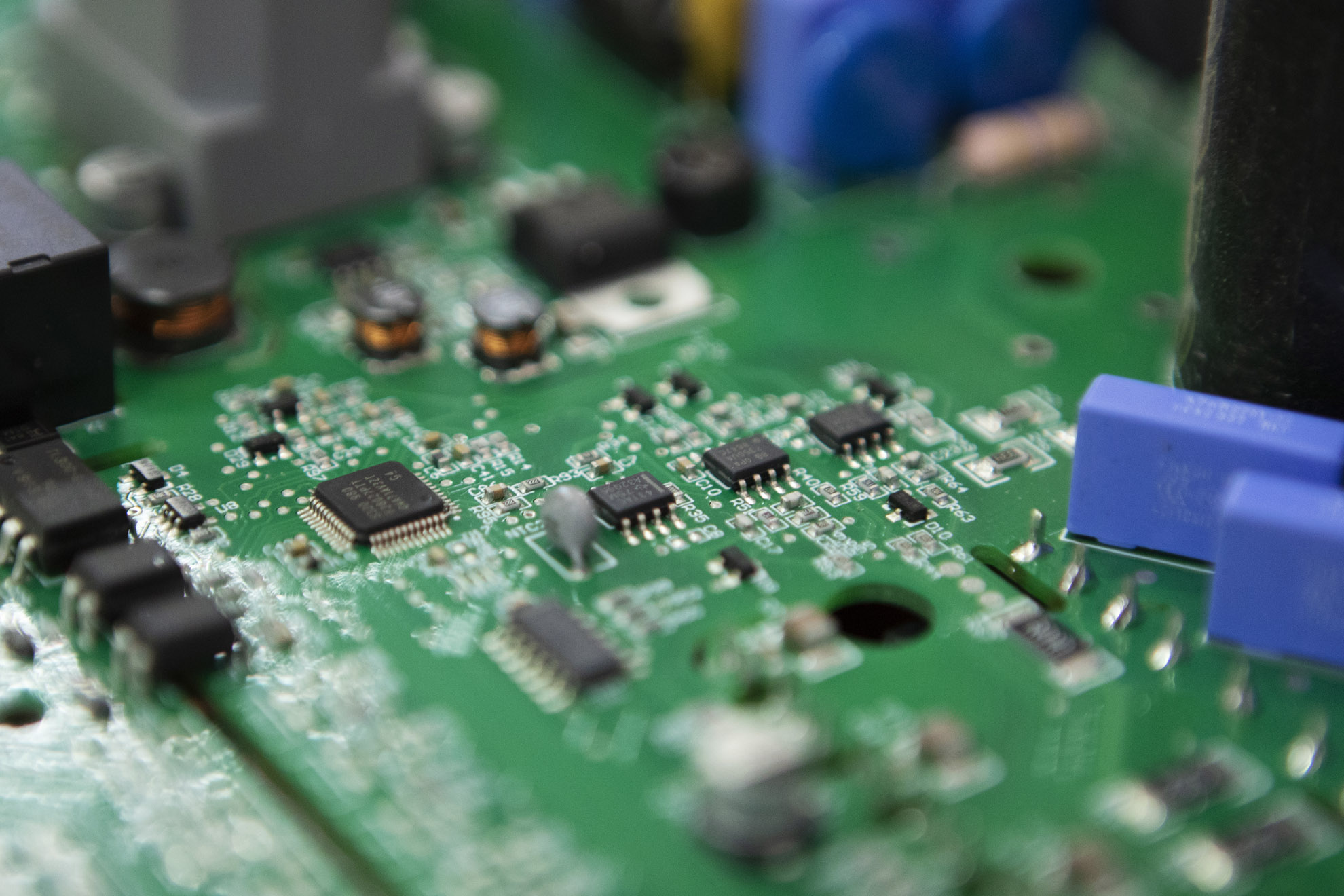
Check up was born in 1991, in a garage in the city of Pordenone. Our payoff is the foundation of Check Up: “Objects with life inside”. We aim at creating objects that contribute to making people’s lives more agile, more functional, new. Being producers allowed us to immediately understand that combining inventiveness and industrial production would be our defining quality. To create actually innovative living objects, we had to be able to invent and implement them at the same time.
Our name represents our operative method: we start with a deep analysis of the clients’ requirements and needs. We can therefore take care of every step: the conceptualization, the project phase (which is always based on the client’s requests), and the production phase. We think of it as a technological check-up. It is the first instrument we have to bring real innovation, both in terms of skills and in implementing available technologies.
Our first project was a wireless anti-theft system, but the need to expand our company’s vision led us to the field of personal care, interior design, and a multitude of projects including environmental sanitation, home development, and smart sensors. In this respect, being able to physically make the technologies we conceptualized allowed us to be both designers and producers. This leads us to the most important aspect of our business concept. Behind all of Check Up’s projects, lies an idea of ethical technology. We focus on projects that can bring benefits to people’s lives and well-being, both in terms of functionality and actual care (i.e. medical devices). In doing so, we follow the principles of circular economy and sustainability.
Step by step, from idea to production
Check Up has always dealt with different areas of application of electronics: since the beginning, the focus has always been on innovation. Our production is as varied as possible and adapted to the needs of the customer.
Check Up was born, in Pordenone.
Construction of the first medical care device.
Opening a new office in Treviso.
Conception of a new technological architecture for wellness; beginning of the collaboration with Jacuzzi.
Creation of the Check Up catalog for the wellness sector, participation in the first ISH international fair in Frankfurt.
Design and construction of the first IP sealed touch screen display for outdoor and wellness use.
Filing of the first patents and trademarks.
Study and realization of electronics for the handling of hospital beds. The first high-efficiency three-phase inverter for Jacuzzi is also produced.
Development and patenting of the i-krome™ system for spas, wellness centers, and the wellness sector in general. Installment of an in-house laboratory for sample reliability tests and life tests on prototypes and serial production.
Creation of capacitive keyboards on glass and related European patent.
Quality certification ISO 9001/2000.
Birth of the internal pre-compliance EMC laboratory.
First LED street lighting systems, Dataenergy brand spinoff.
Design of high-efficiency LED power supplies and control units for solar-powered devices.
Adaptation to ISO 9001/2008.
Development of a touchless keyboard for appliances and medical applications.
Development and design of wireless modules for medical applications and implementation of an OLED device for the lighting sector.
Development of devices and interfaces specific to the medical sector including the first embedded systems.
Development of the first IoT product for medical use for home therapies; the system is connected and monitored by the attending physician.
Capacitive user interface on metal and first IoT device on a wifi/NFC basis for tracking consumables in the vending machine sector.
Launch of the business unit that deals with technological integration in furniture; presentation of the ITAUDIO system certified by Apple.
Apertura ufficio R&D nel Parco scientifico e tecnologico di Udine per lo sviluppo di architetture in ambito IoT e presentazione del primo sistema di fitodepurazione.
Opening of the R&D office in the Science and Technology Park of Udine for the development of architectures in the field of IoT and presentation of the first phytopurification system.
Development of mems and environmental sensor architecture including an NFC-based tracking system for blood banks.
Sensor networks, including high-resolution cameras for intensive crop monitoring.
Study of a line of environmental sanitization products.
Crystal valve radio reissued with current technologies from a 1938 design icon; start of research collaborations with different university departments and related spin-offs.
Start of the “sustainable electronics” program, and an innovation eco-system.
30 years in numbers
22
Patents
6
Trademarked brands
12
Registered aesthetic models
535
Projects
15millions
Pieces produced
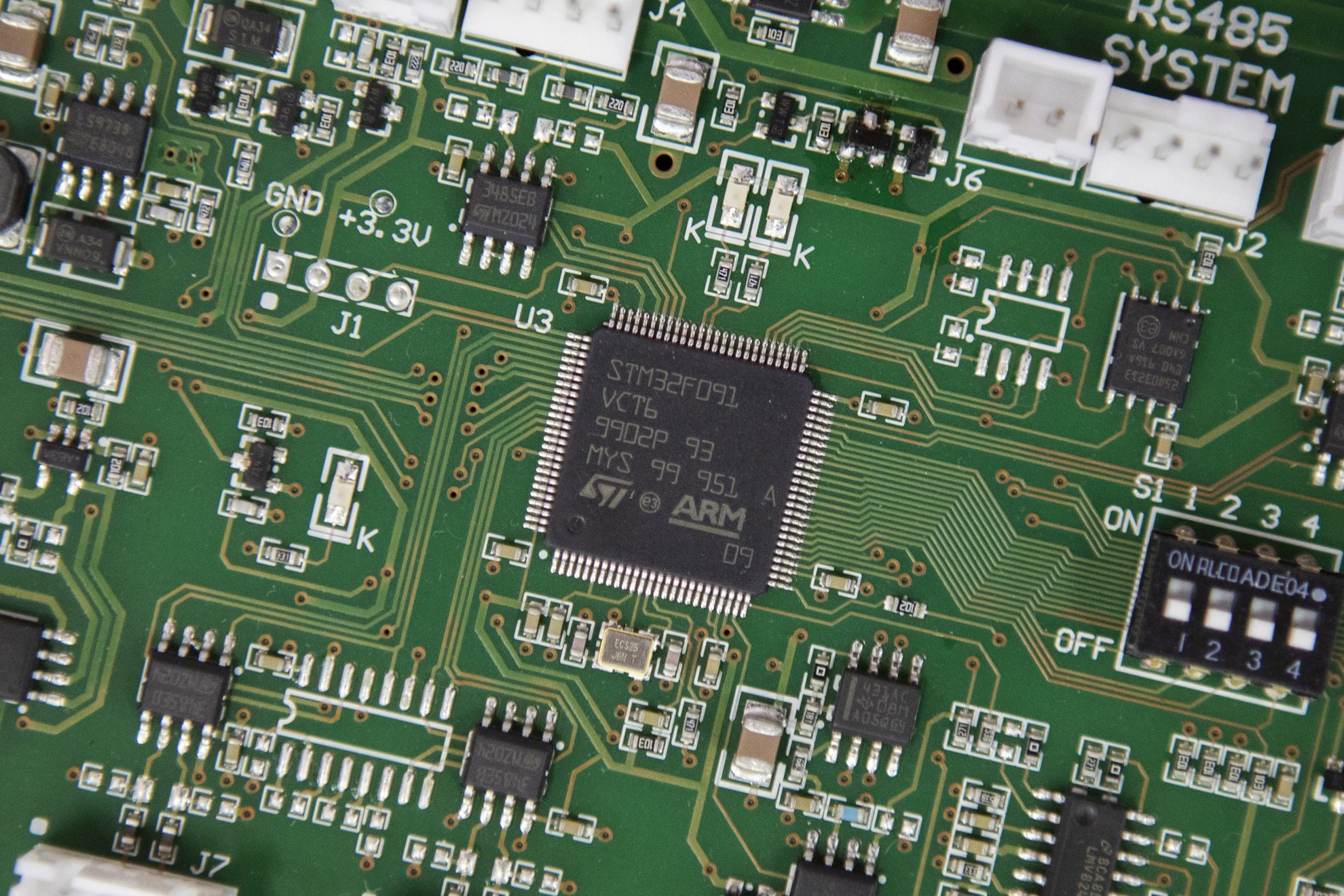
Step by step, from the idea to the production.
Working Steps
01
Concept
The Check Up method starts with a thorough analysis of the client’s needs. Ours is an “innovation funnel” developed through various phases. The first step is to define goals and research the market, alongside the client; following that, we identify the enabling technologies, to evaluate the enhancement factor and the critical issues. Once determined the concept and the budget, we proceed to the realization and production. This method effectively limits the inherent uncertainties of a newly developed technology, allowing us to completely focus on the goals.
02
Design
We implement devices with our native technology, but we also produce on demand. We develop technologically accessible and aesthetically-pleasing products. Reliability and ease of use and installation are the common features of all our projects. We share goals, objectives, and results with our clients. Our goal is to understand your needs first, and then to translate them into pleasing, technologically advanced products. We take painstaking care of the client’s needs like a tailor would: each detail is crafted based on the individual. Aesthetics also play a fundamental role in our projects. Thanks to more than thirty years spent working with internationally renowned brands and designers, we have now become a reference point for the aesthetics and never invasive usability of our technologies. Our solutions follow each products’ and each brand’s aesthetic language.
03
Manufacture
With a staff of more than 200 people, our production capacity can handle the assembly of any electronic or electromechanical component, and their testing. Our products go through a series of rigid tests evaluating the raw materials
04
Tests and certifications
We perform specific tests aimed at determining the overall quality of the project and production reliability. This is why we invested in burn testing, stress testing, and life testing equipment. We also have an internal laboratory for the pre-check of EMC electromagnetic compatibility in emission and immunity, an essential requirement for the marketing of products that include electronic components even outside the European Community. For the supply of finished products, we have an end-of-line test instrument compliant with European directives CEI EN 60335-1 and CEI EN 60204-1 with its digital register of the serial number and batch tested.
05
Step by step, from the idea to the production.
Check Up has always dealt with different areas of application of electronics: since the beginning, the focus has always been on innovation. Our production is as varied as possible and adapted to the needs of the customer.
Contact us!
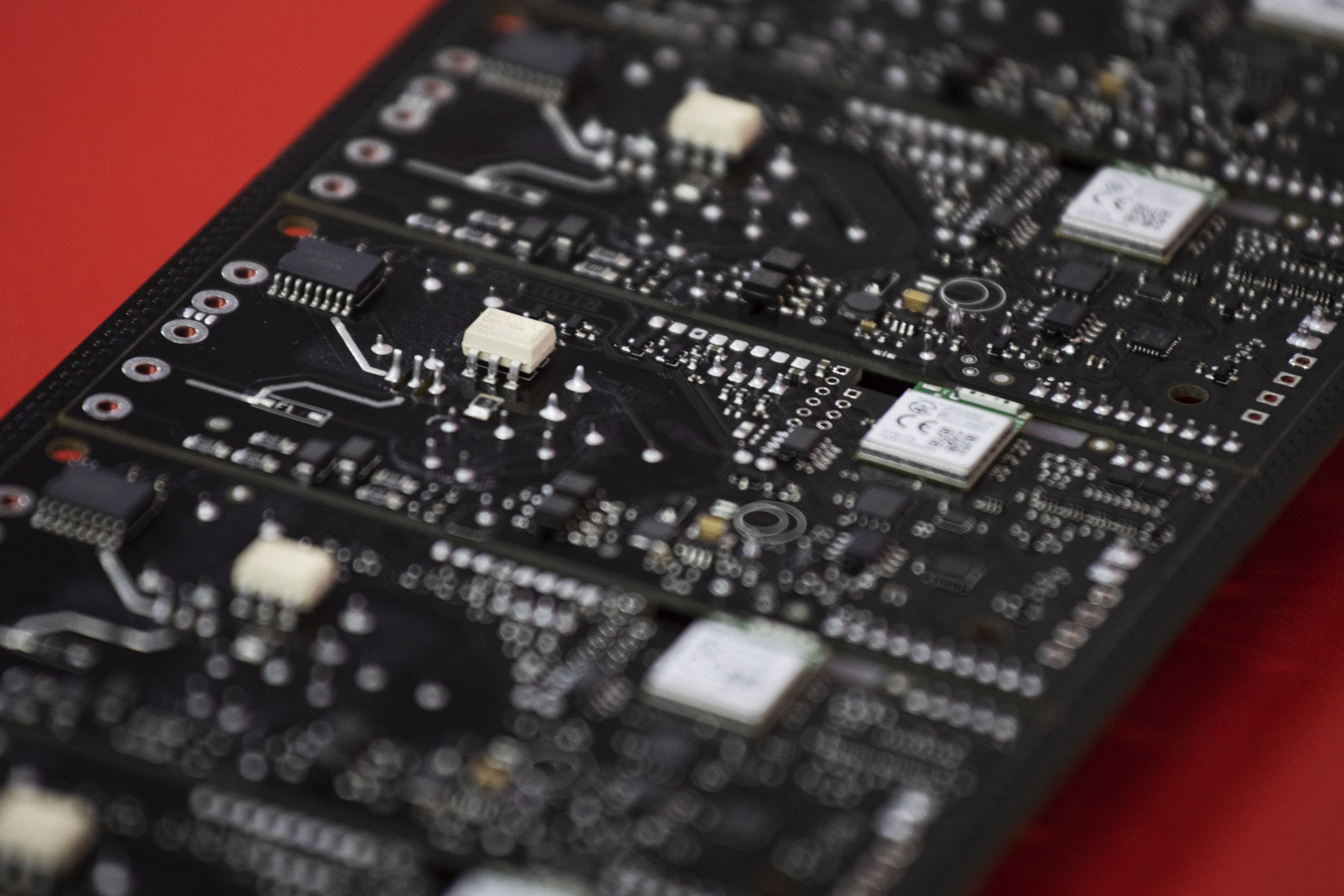
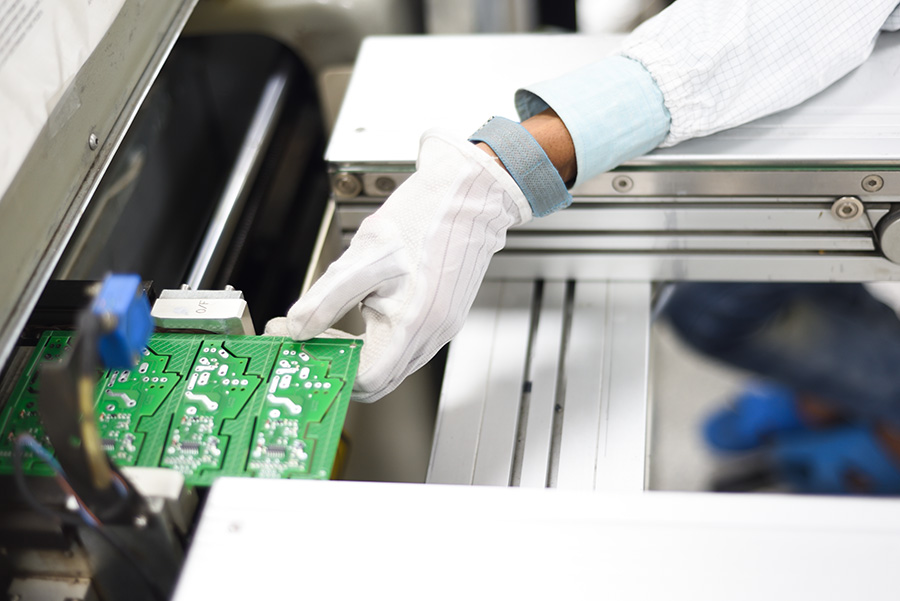
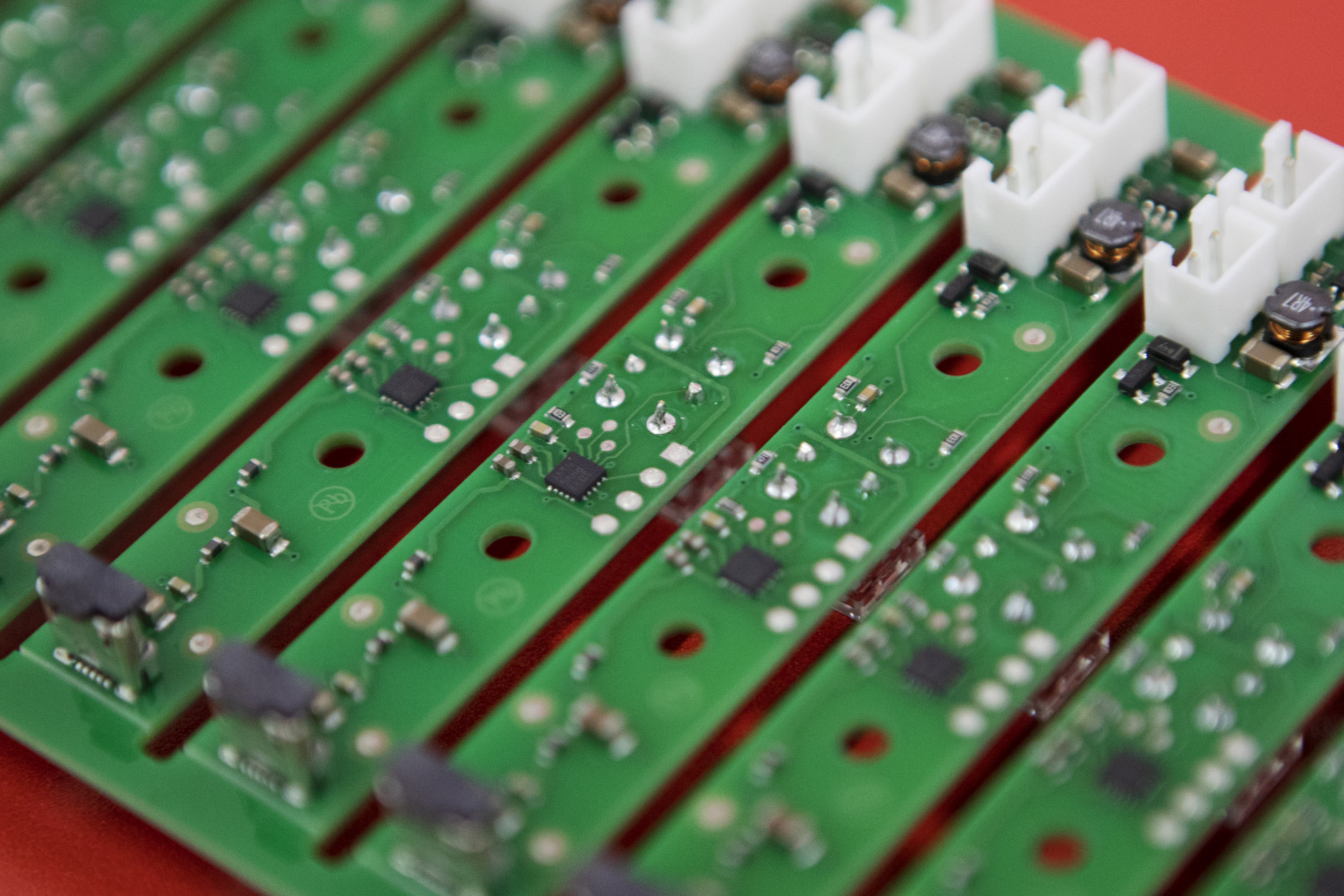
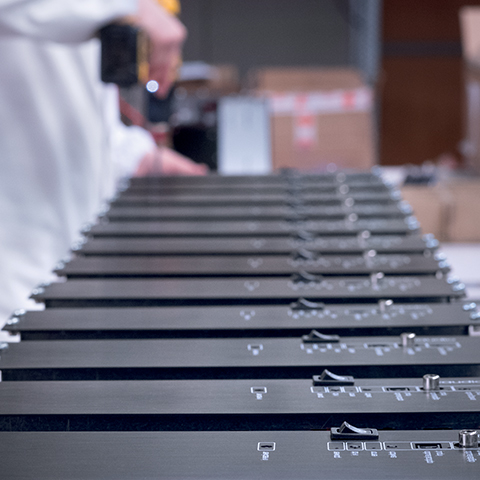
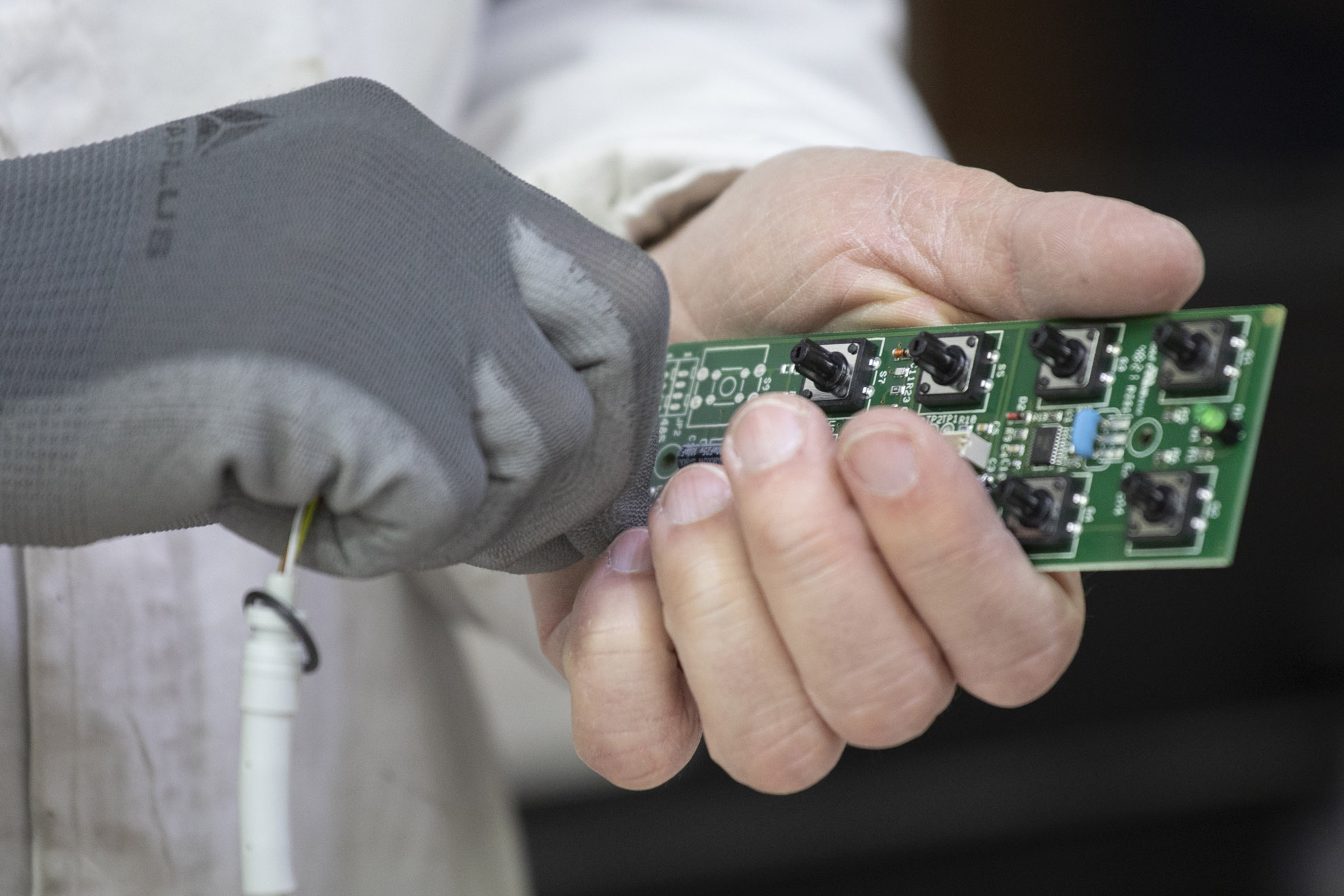
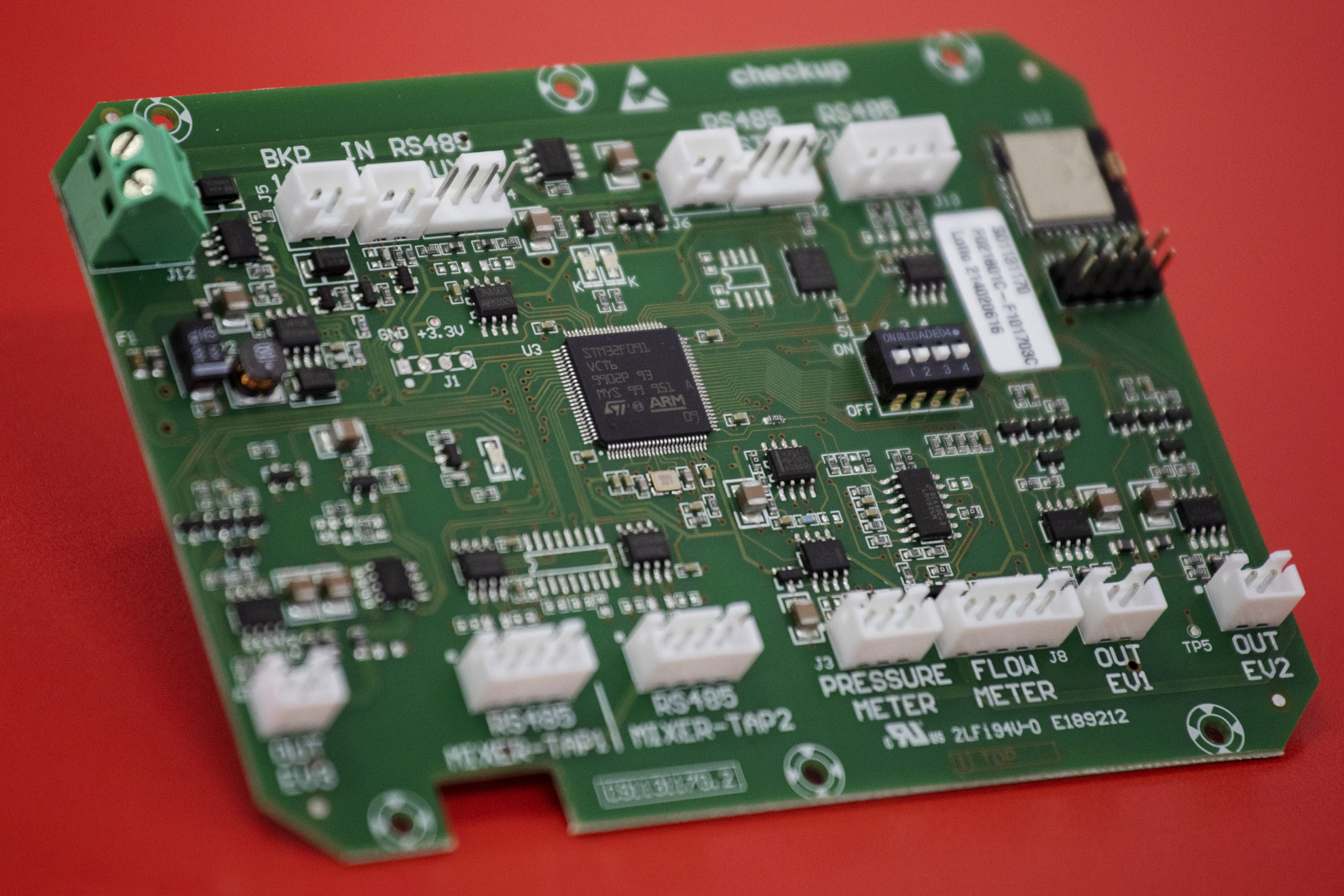
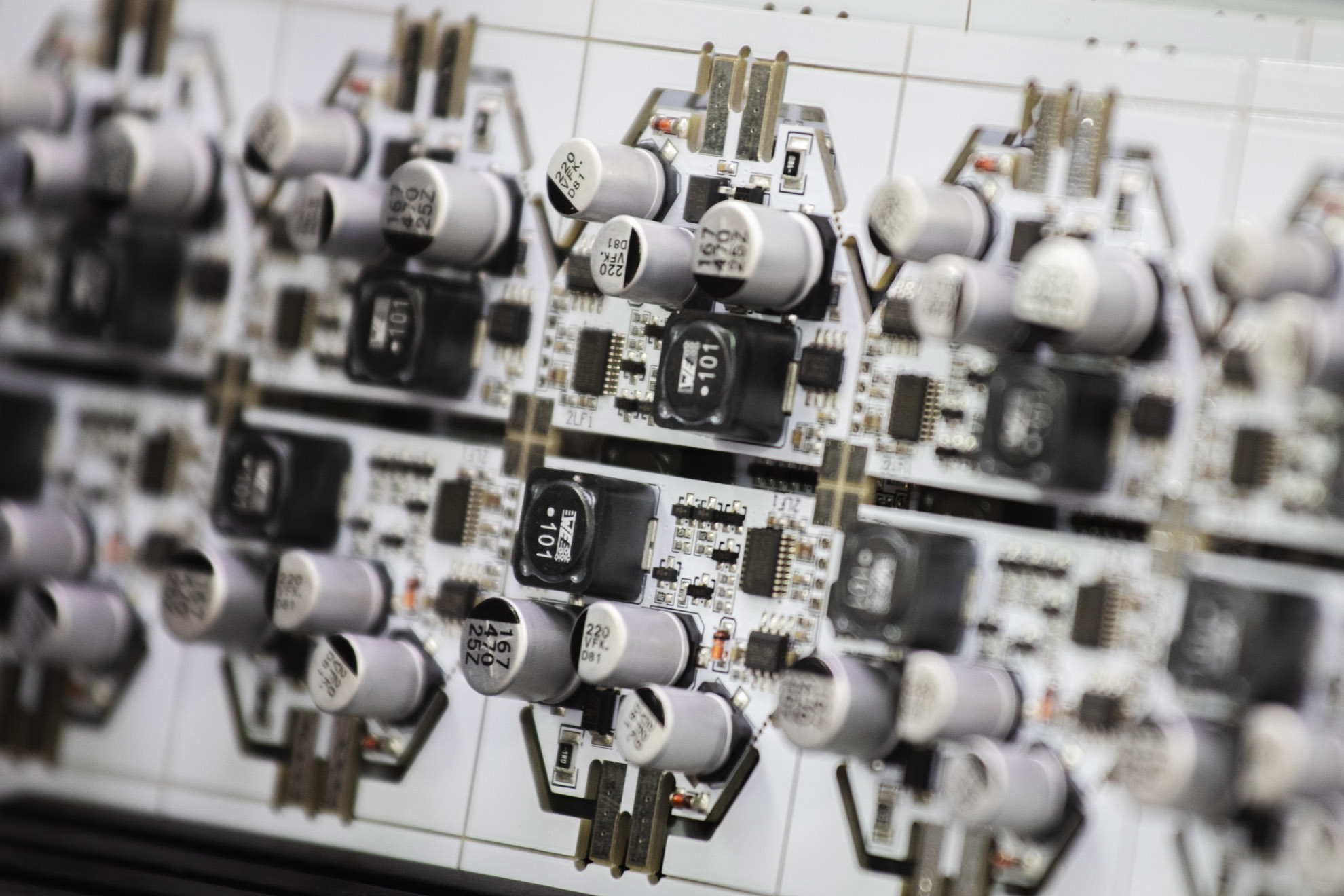